
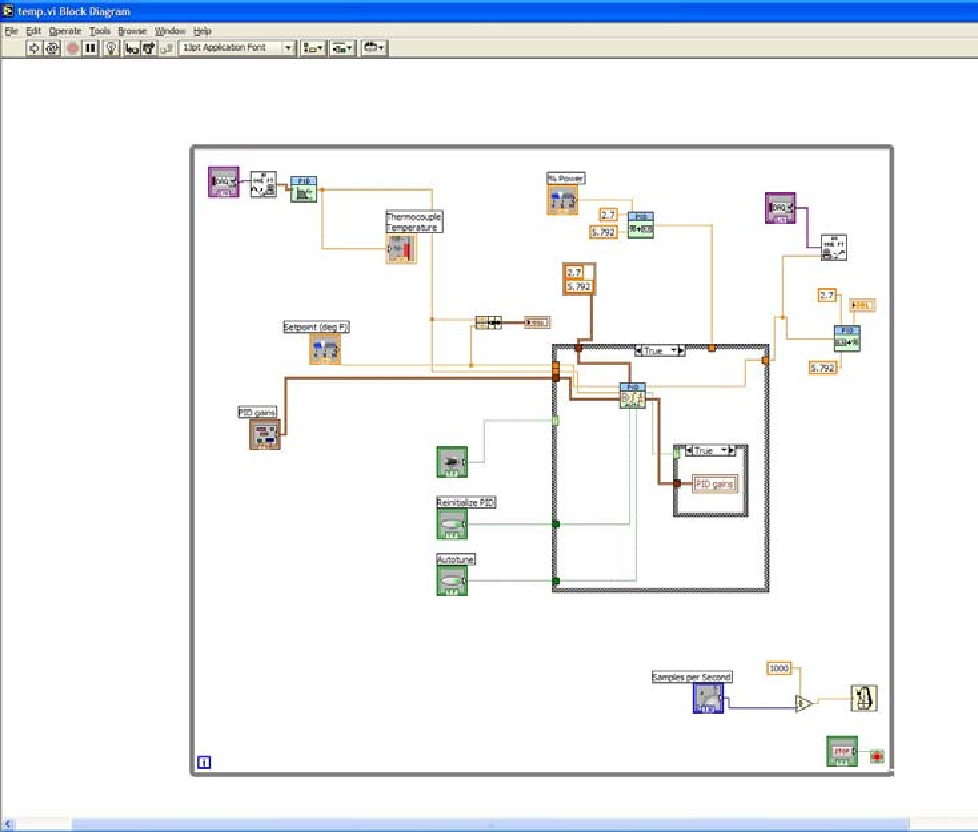
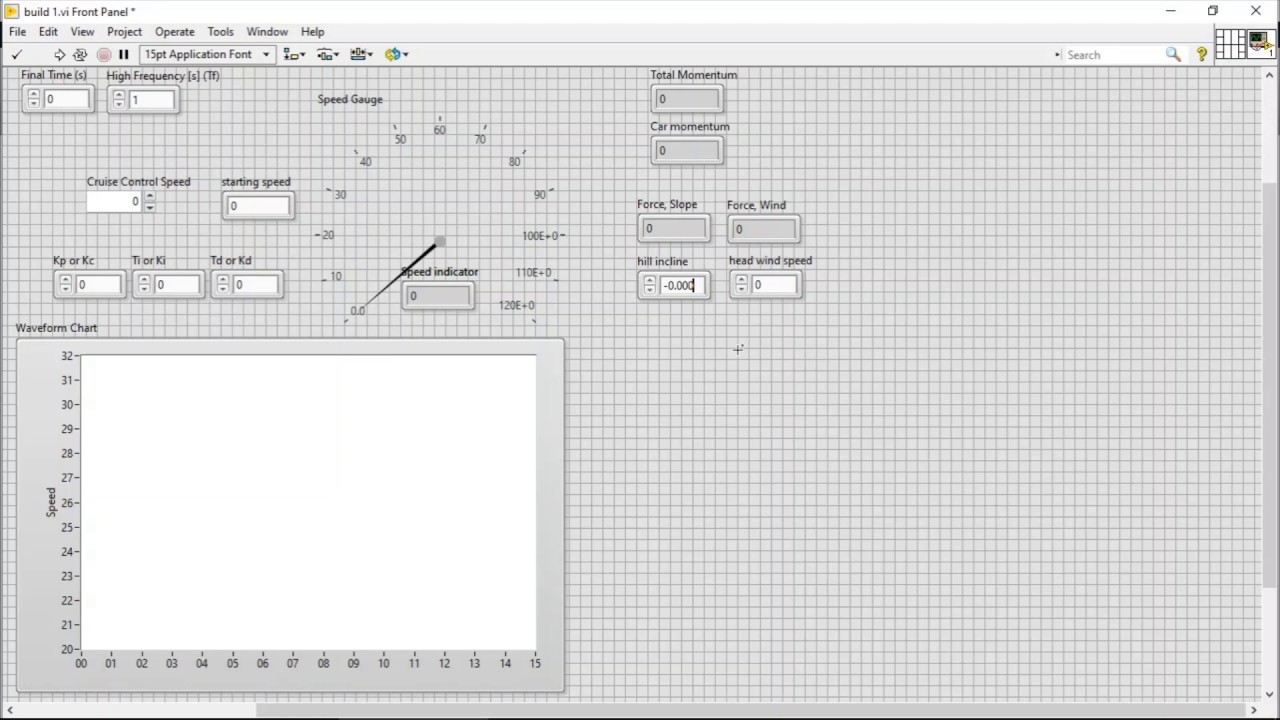
To address this concern, a robust and improved fractional order parallel control structure (FOPCS) for flow control is proposed in this paper. Use of these valves often incorporates nonlinear and uncertain dynamics in the control loop on account of its input-output characteristics, which may result in degradation of control loop performance. This means that the gains from the I and D controller are set to zero so that the influence of P can be determined.Control of flow rate in industrial plants is an essential and crucial task, which is usually achieved by pneumatic control valves in industries.
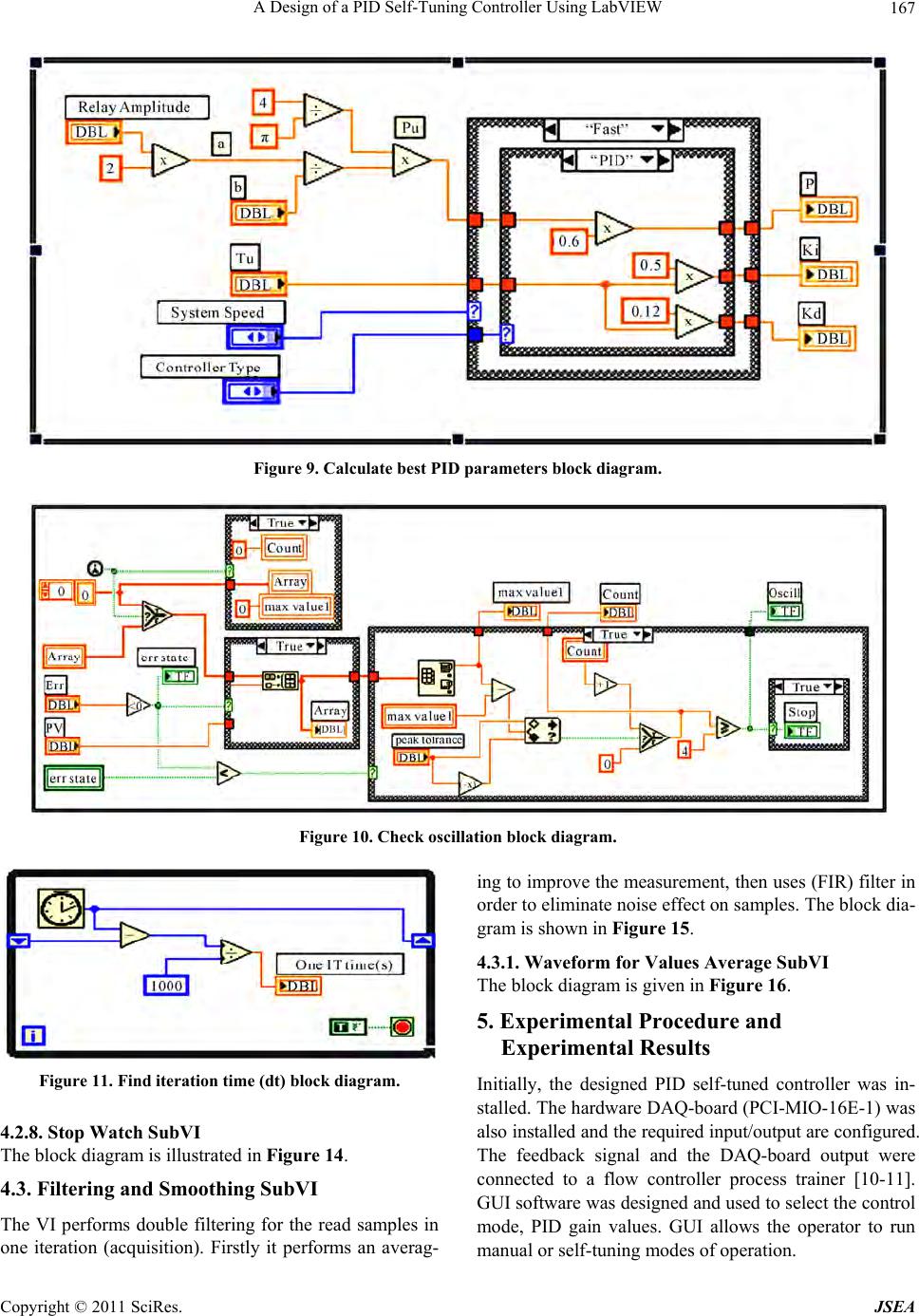
The Ziegler-Nichols closed-loop tuning method is limited to tuning processes that cannot run in an open-loop environment.ĭetermining the ultimate gain value, K u, is accomplished by finding the value of the proportional-only gain that causes the control loop to oscillate indefinitely at steady state.
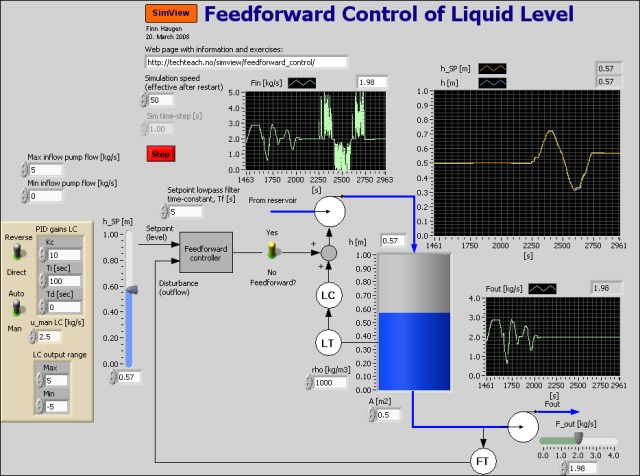
You can obtain the controller constants K c, T i, and T d in a system with feedback. It is a simple method of tuning PID controllers and can be refined to give better approximations of the controller. The Ziegler-Nichols closed-loop tuning method allows you to use the ultimate gain value, K u, and the ultimate period of oscillation, P u, to calculate K c. Ziegler-Nichols closed-loop tuning method To map these parameters to P,I, and D control constants, see Table 2 and 3 below in the Z-N and Cohen Coon sections. In order to find the values for τ dead and τ, a line is drawn at the point of inflection that is tangent to the response curve and then these values are found from the graph. \nonumber \]Īn example for determining these parameters for a typical process response curve to a step change is shown below.
